Case Study - Gas Condensate / Transfer
CASE STUDY
GAS CONDENSATE / TRANSFER
The Job:
The customer’s existing four mechanical sealed pumps had reached their end of life. As the environmental regulations had also become more stringent since the original installation of the pumps, the customer decided to replace the pumps with zero emission magnetic driven pumps. There was an additional desire to increase the flow rate of the pumps during the change. This increased flow led of course to an decrease of the NPSH available, as the condensate has a vapor pressure at roughly atmospheric pressure at 38 °C. A further stipulation was that the installed power should not be changed, as the requirements of installing new power cables would have made that project economically unfeasible.
The Result:
The customer had bad experiences with centrifugal pumps with inducers from other manufacturers, as most inducer designs severely limit the permissible operating window of the pump. Fortunately the Klaus Union Inducer design does not have such limitations. This addressed the concerns regarding the reduced NPSH available due to the increased flow rate.
The next feature essential to resolve the challenge posed by the customer was to equip the pump with a non-metallic isolation shell. With a non-metallic isolation shell no eddy current losses are generated in the magnetic coupling, increasing efficiency of the pump and avoiding any additional heat generation normally associated with magnetic coupled pumps if they are equipped with the standard metallic isolation shells.
The better efficiency of the pump, when compared with the customer’s existing pumps in conjunction with the non-metallic isolation shell allowed the increase of the flow rate without increasing the required motor power, thus avoid allowing the reuse of the existing power cables. Since their successful commissioning in 2016 the pumps have been operated without any downtime for maintenance, providing an uninterrupted availability to the customer.
What is an Inducer?
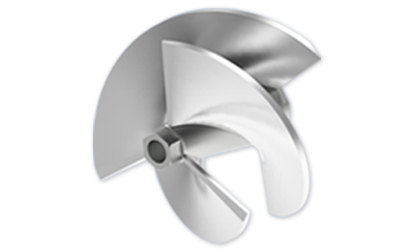
An Inducer is essentially an axial impeller suction stage which is installed on the pump shaft directly in front of the regular impeller.
It has a only a small number of vanes and provides a small head increase. This results in a significant improvement of observed NPSH(R) of the pump. By changing the design of the inducer, the point of best NPSH on the pump performance curve can be further optimized, so it better aligns
with the required operating point of the pump. The Klaus Union inducer design is specifically optimized for each radial impeller to ensure the overall permissible operating range of the pump is not reduced compared to pumps without inducers. It can be retrofitted on existing Klaus Union pumps, in most cases with only a minimum amount of pump modification.
Key Facts:
INDUSTRY: PROCESS: PRODUCT: APPLICATION: SOLUTION: LOCATION: |
UP STREAM OIL & GAS INDUSTRY CONDENSATE STORAGE GAS CONDENSATE TRANSFER CENTRIFUGAL PUMP WITH MAGNET DRIVE NETHERLANDS |
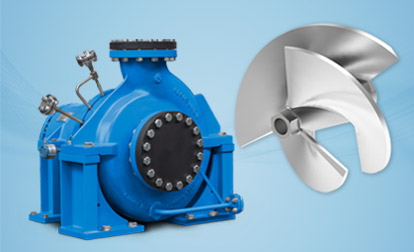
Operating Data:
FLUID: | Gas condensate |
FLOW RATE: | 210 m³/h (925 gpm) |
TEMPERATURE: | -11 ... 28 °C (12 ... 82 °F) |
DELIVERY HEAD: | 38 m (125 ft) |
DYNAMIC VISCOSITY: | 4 CP |
SPECIFIC GRAVITY: | 0,75 |
NPSH(A): | 4,8 m (15,7 ft) |
The Solution: SLM APL 08.0-06.0x15-25E06CJ
SLM: | Sealless Mag Drive |
APL: | Centrifugal pump according API 685 |
08.0: | Nominal Pipe Size of suction flange |
06.0: | Nominal Pipe Size of discharge flange |
15: | Nominal size of impeller |
25: | Magnetic drive size |
E: | Type of magnet |
06: | Length of magnetic drive |
C: | Non metallic isolation shell |
J: | Inducer |