KLAUS UNION MAGNET DRIVE
Sealless Technology
If pumps are used to handle dangerous products, it is essential to avoid even the smallest leakages into the environment in order to ensure the protection of both people and the atmosphere. The ideal solution for such a case is pumps with magnet drive. The first of its kind was introduced by Klaus Union in 1955.
Technical Description
In a magnetic drive pump, the drive shaft – to transfer the mechanical energy from the drive to the pump hydraulics – is not a single shaft with a gland packing or mechanical seal on it. Instead, the energy is transferred contactless from the drive shaft to a pump shaft, using a magnetic coupling. The drive shaft connects the motor with the outer magnet carrier, while the pump shaft holds the inner magnet carrier and the impeller. Both magnet carriers are fitted with permanent magnets, on the inside and the outside respectively. Due to the rotation of the outer magnet carrier, the inner magnet carrier is rotated synchronously via magnetic forces; the mechanical drive energy is transmitted.
Between the magnet carriers, the so-called containment shell is installed to separate the pumped fluid from its environment. The pump shaft is supported by fluid-lubricated maintenance-free slide bearings within the pump’s hydraulic system. There are no dynamic seals between the pumped fluid and the environment from which leakage can escape. Only two static seals are used between pump casing and casing cover and between casing cover and containment shell in the magnetic drive pump.
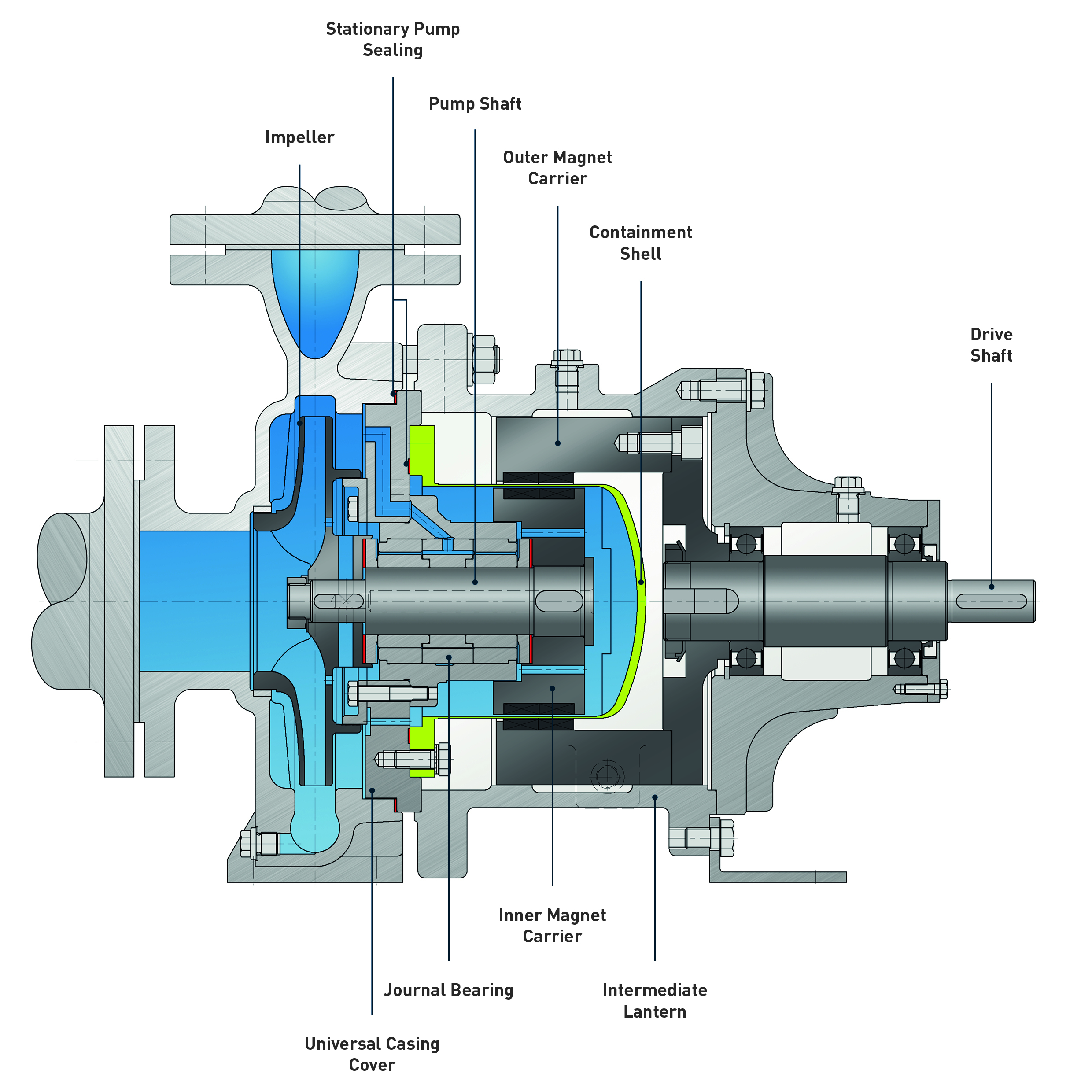
Advantages vs. Mechanically Sealed Pumps
- Nearly maintenance free
- Less investment costs and less maintenance costs
- No instrumentation or special monitoring devices required in standard
- No utilities required, such as nitrogen or cooling water
- No leakage to the atmosphere
- No loss of sealant liquid
- No wear of the seals at all
- Low mechanical loads on shaft and bearings
- High stiffness of the pump shaft
Advantages vs. Canned Motor Pumps
- Standard IEC and NEMA motors can be used
- Lower investment and repair costs
- Separate flushing of journal bearing
- Higher efficiency
- Use of non- metallic containment shell possible
- No heat generation of the rotor by electric losses
- Higher viscosities possible
- Higher temperatures without cooling possible
- No special monitoring devices necessary