Flow Rate
max. 1.800 m³/h
Differential Pressure
max. 40 bar
Temperature Range
-120 °C to +350 °C
Pressure Rating
max. PN 400
KEY FACTS
-
According to API 676, 3rd Edition
-
Maintenance-Free Permanent Magnet Drive
-
Modular Design
-
Cartridge Design
-
Modular Construction (Multi-Part-Casing)
-
Adaptive Feet with Centerline Mounting
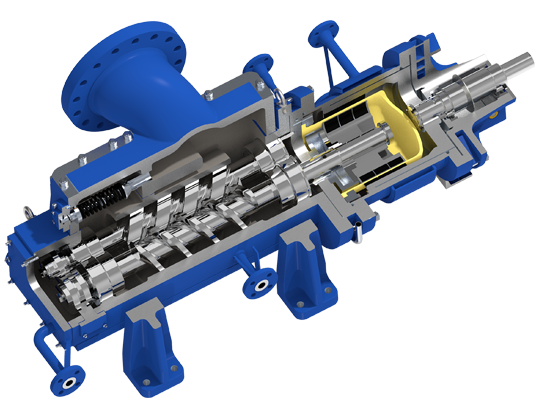










DESIGN
- Single Volute Twin Screw Pump in Process or in Tank Farm Design
- Axial Split Modular Casing
- Pressure Limiting Valve using Klaus Union Valve Series Internals
- Centerline Mounting
- Permanent Magnet Drive
- Easy to maintain
- Seperation of Liquid Chamber and Atmosphere by Means of Containment Shell
- Magnet Drive acc. API 685 available
- High Viscosity optimized design available
- Bearing Bracket with Oil-Lubricated or Greased-for-Life Anti-Friction Bearings; optional: Close-coupled design (SLM DSP-2CB)
- Spare parts of magnetic coupling and bearing brackets are interchangeable with centrifugal pump series
OPERATING RANGE
Performance Range | |
Flow Rate | Q= max. 1.800 m³/h |
Differential Pressure | P= max. 40 bar |
Viscosity | max. 100.000 mm²/s (cSt) |
Higher Flow Rates upon Request
Pressure Ratings | |
Standard Construction | PN 25 at +120 °C |
Temperature Range | t= -120 °C to +350 °C |
Pressure Rating | P= max. PN 400 |
Higher Pressure Ratings upon Request
TYPICAL APPLICATION
- Acids
- Lyes
- Hydrocarbons
- Bitumen / Asphalt
- Tar
- Fuel Oils (Light and Heavy)
- Polymers
- Aggressive, Explosive and Toxic Liquids
- Liquids Containing Solids
- High-Viscosity Liquids
CUSTOM MATERIALS
Pump Casing | Cast Carbon Steel; Cast Stainless Steel; Duplex Stainless Steel; Super Duplex Stainless Steel |
Liner | Cast Carbon Steel; Cast Stainless Steel; Duplex Stainless Steel; Super Duplex Stainless Steel; Wear Resistant Coating |
Rotors | Carbon Steel, nitrated; Martensitic Stainless Steel, nitrated; Stainless Steel, hardened; Duplex Stainless Steell, hardened; Wear Resistant Coating |
Containment Shell | Hastelloy C; Titanium; Alloy 718; Zirkonium Oxide |
Upon Request, Klaus Union Screw Pumps, Series SLM DSP-2C, can be supplied also in Hastelloy, Inconel, other High Nickel Alloys or Titanium.
DESIGN VARIANTS
A heat jacket (H3) around the bearing lantern causes a heating of the magnet drive.
The pumps are outfitted with a foot heating (H4) and/or a heat jacket in the bearing lantern (H2). Both can be realized either separately or in conjunction with a bypass line. Both heating systems are rated for operating pressure of 16 bar at 200 °C (steam) or 6 bar at 350 °C in the standard construction. They can also be used for cooling.
The thermal barrier acts as a structural element between the bearing carrier (in the bearing carrier model) or drive motor (in the close coupled model), whereas the hydraulic system allows for heat transfer. This reduces ball bearing temperatures in the gearing when hot liquids are being transported. A radial shaft sealing ring can also be integrated into the thermal barrier for purposes of sealing the magnet driver. The sealing ring acts as a secondary seal that prevents the product from leaking into the environment through a leak in the isolation shell. In order for this secondary seal to be used, the magnet driver chamber must be monitored so that leaks can be detected in good time.
When solids-containing liquids are being transported, the internal filter prevents inadmissibly large particles from entering the flow channels, and from there the magnetic coupling and internal bearings.
This isolation shell generates no Eddy Current losses in the magnet drive. This isolation shell offers maximum pump effi ciency and is particularly benefi cial where heat input into the pumped liquid is to be avoided.
The plastic isolation shell consists of two separate components â?? a carbon fi bre reinforced outer shell, and an inner PTFE liner. The shell eliminates Eddy Current losses and is used to maximise the pumpâ??s over-all efficiency, or when a temperature rise of the internal flush flow must be avoided.
These external connections allow for external flushing, feeding and/or venting. Connection E1 is used in situations where a continuous feed into the magnet drive is desired. Connection E2 is used suitable for short-term flushing, or for external venting of the magnetic coupling.
The self-cleaning discharge fi lter is used for applications where liquids with a moderate percentage of solids are handled. The flush flow is picked up externally from the discharge filter and re-introduced into the magnet coupling. The internal flush flow ports are closed.
This construction type is used for applications where liquids with a high percentage of solids are handled. The casing cover is equipped with two external connections for feeding and draining of the isolation shell area. The specially designed journal bearings prevent any solids within the pumped liquid from entering the magnet drive.
The double isolation shell should be used in situations requiring a high level of safety. The unit consists of two interlocking isolation shells, both of which are rated for the relevant operating conditions. If one of the two units is damaged, the casing still remains leaktight. The gap between the two units can be monitored.
The secondary sealing consists of a highperformance radial shaft seal ring, which ensures that there is no immediate leakage of the liquid to the atmosphere in the drive shaft area in the event of an isolation shell failure.