FIVE OFFSET
BUTTERFLY VALVES
The same designer who invented and patented the four offset butterfly valve in 2008 is introducing now the newest evolution in butterfly valve design. The first butterfly valve in the world which is not using a regular cone for it´s seat design.
In the newly designed V-AXX® valve, the seat shape can be changed around the whole seat without restrictions. If necessary, the angle of the seat, even in the shaft area, can be 25° or more, without changing the angle in other areas. This is only possible due to the unique seat design, which is not formed by a simple cone but by a much more complex figure, not yet named in geometry.
LATEST TECHNOLOGY IN BUTTERFLY VALVES DESIGN
In previous designs, the seat shape never changed along its 3D figure, but in the newly invented design, the lines forming the outside shape do not cross in the same point as in a cone. Basically, this means the designer is free to design the seat angle all the way around the seat. If necessary, the shaft offset from the pipe centerline could be brought to zero and still produce a friction-free valve.
Our Product Range
V-AXX® CRYOGENIC
The research conducted in the Dr. Gaida R&D Institute has provided an initial evaluation of the real shrinkage rates in cryogenic temperatures
as a function of the wall section and allowed the seat to be formed accordingly making the valve zero leakage from -270 °C up to 1800 °C, from vacuum up to 160 bar, from liquid nitrogen up to liquid sodium.
THE PERFECT SOLUTION FOR YOUR APPLICATION
PERFORMANCE DATA
- DN 50 up to DN 2100
- 2" up to 84"
- PN 10, 16, 25, 40, 63, 100, 160
- ANSI 150, 300, 600, 900
- Fully rated Delta P in both directions
- Temperature -270 °C up to 1.800 °C
STANDARDS
- ISO 9001
- PED 2014/68/EU
- DIN EN 12516, DIN 3840
- ASME B 16.34
- AD 2000
- AD W10
- BAM (Oxygen Approval)
- TA Luft
- NACE MR 0175, NACE MR 0103
- 94/9 EG ATEX
SPECIAL SOLUTIONS
- Sealed bearing design
- Monitoring port
- Shaft extensions
- Steam jacket
ORCA®
ELIMINATING THE RISKOF CAVITATION
The new ORCA® trim provides huge advantages against other solutions. Plates mounted on both sides of the disc allow the pressure to drop in several stages and prevent supersonic speed in gases and prevent the cavitation in liquids. One or more sets of plates can be mounted in accordance to the customer needs, allowing an excellent flow control when the valve is partially open.
Since the plates are mounted parallel to the disc and moved together with the disc, they do not interfere with the flow when the valve is fully open. This ensures the maximum Kv / Cv value remains as this of a standard valve.
LATEST TECHNOLOGY IN BUTTERFLY VALVES DESIGN
In previous designs, the seat shape never changed along its 3D figure, but in the newly invented design, the lines forming the outside shape do not cross in the same point as in a cone. Basically, this means the designer is free to design the seat angle all the way around the seat. If necessary, the shaft offset from the pipe centerline could be brought to zero and still produce a friction-free valve.
ADVANTAGES
- Better flow control
- No cavitation
- No supersonic speed
- Lower noise level
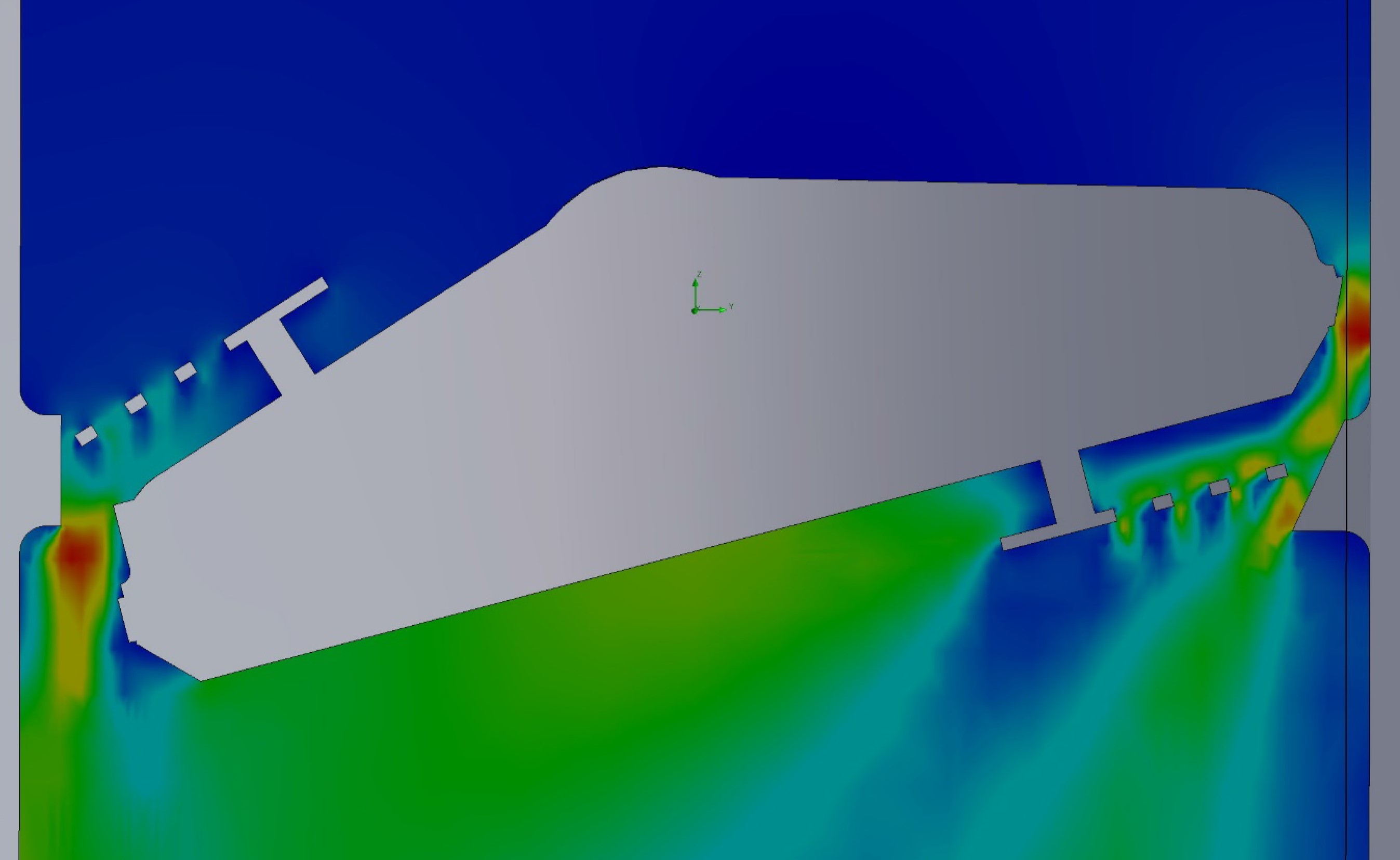
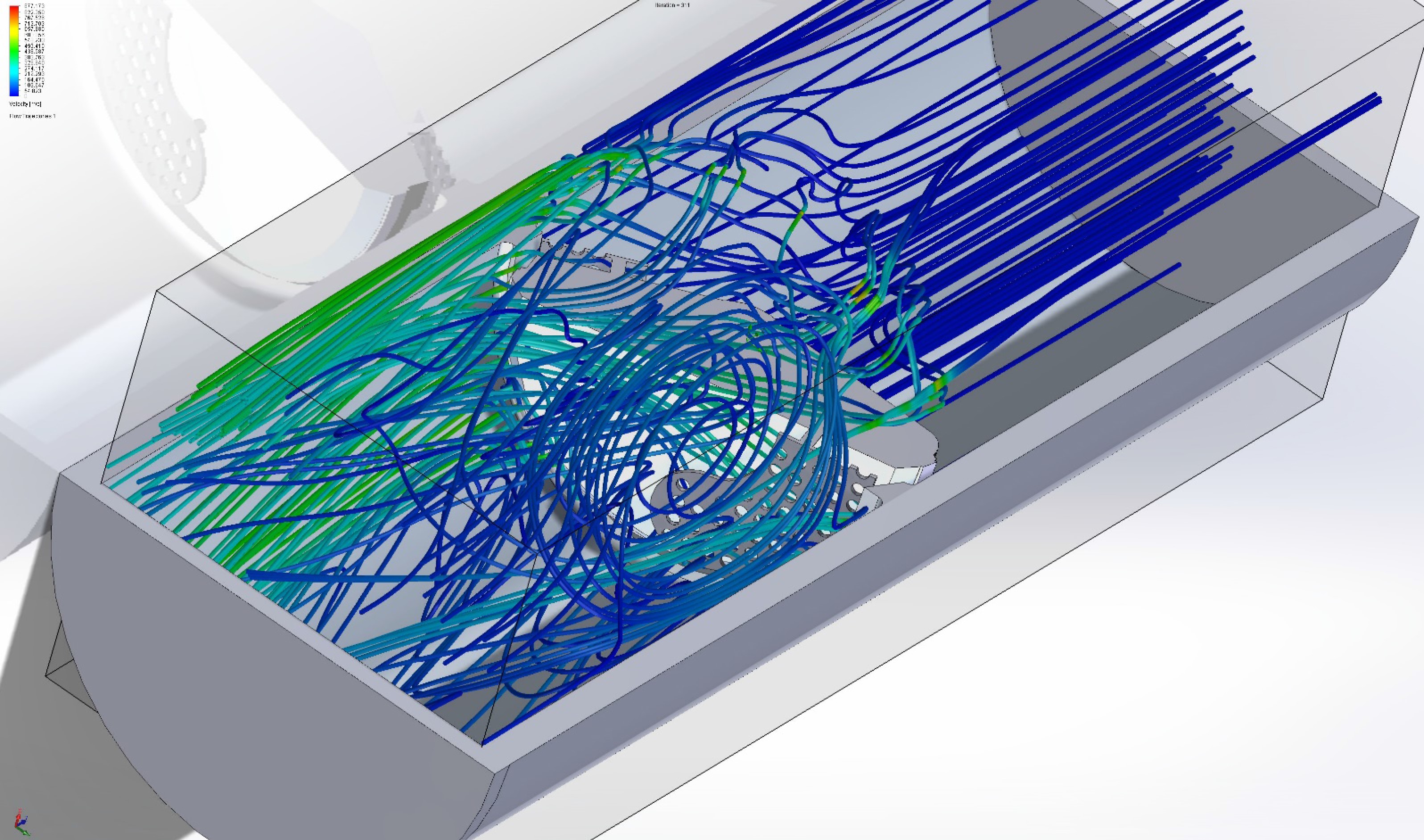
Kv / Cv Values
The V-AXX® valve has the highest Kv / Cv of any comparable torque-seated butterfly valve. Not only the valve can be sized smaller. Even the actuator, the piping as well as the entire construction supporting the piping can be sized smaller. Consequently, the costs can be reduced significantly.
With regards to day to day valve replacement where the pipe size and infrastructure have already been determined, the higher flow coefficients with the V-AXX® valve can improve the process performance and lower pumping costs due to the lower pressure drop across the valve.