CASE STUDY - GAS CONDENSATE / TRANSFER
CASE STUDY
GAS CONDENSATE / TRANSFER
The Job:
The customer’s existing four mechanical sealed pumps had reached their end of life. As the environmental regulations had also become more stringent since the original installation of the pumps, the customer decided to replace the pumps with zero emission magnetic driven pumps. There was an additional desire to increase the flow rate of the pumps during the change. This increased flow led of course to an decrease of the NPSH available, as the condensate has a vapor pressure at roughly atmospheric pressure at 38 °C. A further stipulation was that the installed power should not be changed, as the requirements of installing new power cables would have made that project economically unfeasible.
The Result:
The customer had bad experiences with centrifugal pumps with inducers from other manufacturers, as most inducer designs severely limit the permissible operating window of the pump. Fortunately the Klaus Union Inducer design does not have such limitations. This addressed the concerns regarding the reduced NPSH available due to the increased flow rate.
The next feature essential to resolve the challenge posed by the customer was to equip the pump with a non-metallic isolation shell. With a non-metallic isolation shell no eddy current losses are generated in the magnetic coupling, increasing efficiency of the pump and avoiding any additional heat generation normally associated with magnetic coupled pumps if they are equipped with the standard metallic isolation shells.
The better efficiency of the pump, when compared with the customer’s existing pumps in conjunction with the non-metallic isolation shell allowed the increase of the flow rate without increasing the required motor power, thus avoid allowing the reuse of the existing power cables. Since their successful commissioning in 2016 the pumps have been operated without any downtime for maintenance, providing an uninterrupted availability to the customer.
What is an Inducer?
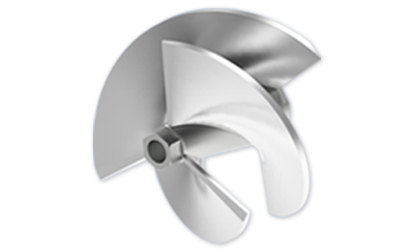
An Inducer is essentially an axial impeller suction stage which is installed on the pump shaft directly in front of the regular impeller.
It has a only a small number of vanes and provides a small head increase. This results in a significant improvement of observed NPSH(R) of the pump. By changing the design of the inducer, the point of best NPSH on the pump performance curve can be further optimized, so it better aligns
with the required operating point of the pump. The Klaus Union inducer design is specifically optimized for each radial impeller to ensure the overall permissible operating range of the pump is not reduced compared to pumps without inducers. It can be retrofitted on existing Klaus Union pumps, in most cases with only a minimum amount of pump modification.
Key Facts:
INDUSTRY: PROCESS: PRODUCT: APPLICATION: SOLUTION: LOCATION: |
UP STREAM OIL & GAS INDUSTRY CONDENSATE STORAGE GAS CONDENSATE TRANSFER CENTRIFUGAL PUMP WITH MAGNET DRIVE NETHERLANDS |
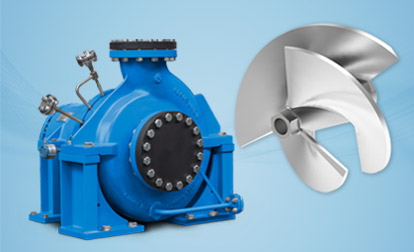
Operating Data:
FLUID: | Gas condensate |
FLOW RATE: | 210 m³/h (925 gpm) |
TEMPERATURE: | -11 ... 28 °C (12 ... 82 °F) |
DELIVERY HEAD: | 38 m (125 ft) |
DYNAMIC VISCOSITY: | 4 CP |
SPECIFIC GRAVITY: | 0,75 |
NPSH(A): | 4,8 m (15,7 ft) |
The Solution: SLM APL 08.0-06.0x15-25E06CJ
SLM: | Sealless Mag Drive |
APL: | Centrifugal pump according API 685 |
08.0: | Nominal Pipe Size of suction flange |
06.0: | Nominal Pipe Size of discharge flange |
15: | Nominal size of impeller |
25: | Magnetic drive size |
E: | Type of magnet |
06: | Length of magnetic drive |
C: | Non metallic isolation shell |
J: | Inducer |
Klaus Union Article
Article - PROCESS TECHNOLOGY & COMPONENTS 2020
Optimizing MTBM and MTBF in unloading stations through the use of magnetic drive pumps
Operators of unloading stations can significatly reduce operational and maintenance cost by using modern magnetic drive centrifugal pumps.
How this works we describe in an article, published in issue 2020 of Process Technology and Components.
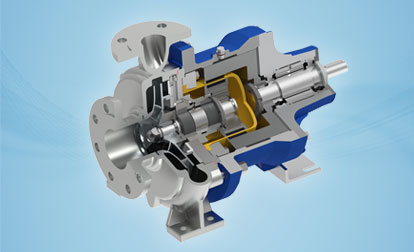
Magnet Drive Centrifugal Pump in Dry Running Design
ZERO EMISSION
Zero Emission
As a manufacturer and inventor of zero-emission magnetically driven pumps, we are proud that we now have our first zero-emission company car in use. The Hyundai Nexo is a hydrogen fuel cell powered crossover SUV. The drive concept uses a fuel cell to generate electricity from hydrogen stored at 700 bar and uses this to power the vehicle by means of an electric motor. The only emission is clean water. The Fuel Cell Electric Vehicle (FCEV) has a nominal range of 600 km and can be refuelled in just 5 minutes.
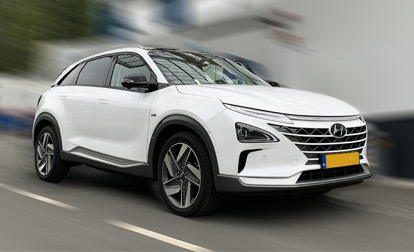
ADIPEC 2019
ADIPEC 2019 // Abu Dhabi
We would like to thank you very much for visiting our stand at this year’s ADIPEC 2019. Once again it has been proven that personal contact is the basis for a good cooperation. We hope you had a successful time at the fair and interesting discussions at our stand.
We would be pleased to welcome you again soon!
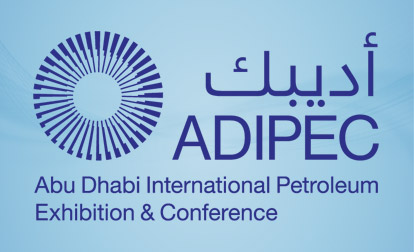
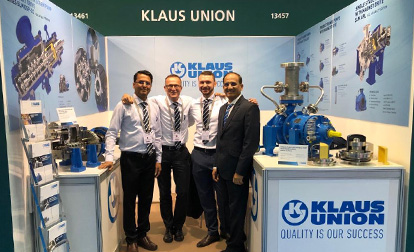
CASE STUDY - BITUMEN/ASPHALT REFINERY
CASE STUDY
BITUMEN / ASPHALT REFINERY
Bitumen/Asphalt pumps in this refinery were considered bad actors due to failing mechanical seals. Klaus Union solved that problem with API 676 and 685 compliant twin screw pumps.
The Job:
The customer, a large refinery in France, was looking to extend its Bitumen handling capabilities by building a new Bitumen storage and loading facility. Existing installations utilized screw pumps from various manufactures. Shaft sealing was done with mechanical seals or gland packing, both with steam quench. Main objectives of the new project were to improve availability of the pumps and to substantially reduce OPEX, especially those associated with maintenance. Additionally the solution should be up to date in regards to current and foreseeable health and safety and environmental regulations. Klaus Union provided engineering and technical studies, comparing different solutions for the customer’s application.
The Thought Process:
All existing Bitumen pumps in that refinery were classified as “bad actors” due to high leakage rates and short seal lifetimes. Based on this existing experience, the following iterations were taken during the pre-engineering phase of the project:
- Bitumen / Asphalt is prone to cracking when it reaches the atmosphere. Accordingly seals should be executed with API Plan 62 (steam quench), requiring additional utilities. Even under ideal conditions an API Plan 62 does not prevent leakage to the atmosphere, making the pump installation always a dirty spot. Additionally Steam supply may sometimes fail or be outside permissible range, leading to regular seal damage and pump downtime.
- Double acting mechanical seal with an API Plan 53 or 54 system were evaluated next. An API Plan 53/54 system does not have the same problems as a steam quench as it provides a stable, pressureized barrier system preventing any Bitumen leakage to the outside. However with a Bitumen / Asphalt application the seal supply system would need to cover both sufficient pre-heating to prevent stocking of the product, as well as sufficient cooling capacity to prevent overheating of the barrier fluid system. This means to ensure a stable operation numerous signals (temperature, pressure, etc.) and utilities (cooling water or energy for an air cooler, nitrogen for API Plan 53, etc.) are required, making this an expensive investment if not for the pump, then for the site.
- Based on existing experience in handling difficult to seal and even toxic liquid, Klaus Union recommended a solution for the customer’s needs, by executing the pump with seal less magnetic coupling system from Klaus Union. The magnetic coupling is equipped with a non-metallic isolation shell, to avoid eddy current losses and provides a pressure rating of 25 bar for the complete pump.
The pump only requires two signals – a temperature transmitter on the isolation shell to provide a startup interlock to ensure proper pre-heating temperature, and a PT100 on the casing to ensure the maximum temperature for the pump is not exceeded. Otherwise no additional accessories are required, and the product is not contaminated by any auxiliary fluids.
The Result:
Two pumps were installed and have been in operation without any downtime for maintenance. The satisfied customer has started a project to replace his existing old pumps with Klaus Union magnet drive twin screw pumps.
Key Facts:
INDUSTRY: PROCESS: PRODUCT: APPLICATION: SOLUTION: LOCATION: |
REFINERY BITUMEN STORAGE AND LOADING FACILITY BITUMEN / ASPHALT CIRCULATION, TRANSFER & LOADING TWIN SCREW PUMP WITH MAGNET DRIVE FRANCE |
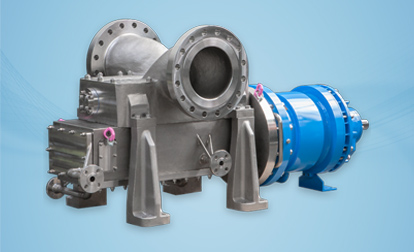
Operating Data:
FLUID: | Bitumen / Aspahlt |
FLOW RATE: | 135 m³/h (594 gpm) |
TEMPERATURE: | 140 ... 180 °C (284 ... 356 °F) |
DIFFERENTIAL PRESSURE: | 12 bar (174 psi) |
DYNAMIC VISCOSITY: | 104 ... 855 cP |
KINEMATIC VISCOSITY: | 110 ... 900 mm²/s |
SPECIFIC GRAVITY: | 0,95 |
NPSH(A): | 4,9 m (16 ft) |
The Solution: SLM DSP-2CO 154B-208-25P14 Q2 Z H24
SLM: | Sealless Mag Drive |
DSP-2: | Single Volute Twin Screw Pump |
C: | Cartridge Design |
O: | Oil Lubricated Bearing Support |
154: | Outer Diameter of Drive Rotor (approx. 6“) |
B: | Axial Split Modular Casing |
208: | Pitch of Main Drive Rotor (approx. 8 1/5“) |
25: | Magnetic Coupling Size (approx. 10“) |
P: | High Powered Magnets |
14: | Magnet Length |
Q2: | Magnetic Coupling Designed for low and high viscosity application |
Z: | Non-Metallic Isolation Shell |
H24: | Casing and Casing Cover Heated |
The Benefits:
- Eliminating „bad actor“ No. 1: mechanical seal
- Maintenance and Leak-free magnetic coupling, eliminating costs for steam quench or API Plan 53/54 Systems
- Robust API 676 compliant pump design to incresae MTBF
- Pump design adaptive to customer requirements
- Continuously high pump efficiency, even at large variations of pressure and viscosity
- No timing required after maintenance, decreasing downtimes for maintenance
- High standardization for fast availability of spares, many available directly from stock
- Modular system for pump and magnetic coupling can be adapted to customer‘s and application requirements
The SLM DSP-2C provides a simpler, cleaner solution to the customer’s needs for highly reliable and highly efficient positive displacement pumps.
Valve World Expo
Valve World Expo
Thank you for your visit
We would like to thank you for for visiting our booth at the Valve World Expo 2018. We hope, that the exhibition was interesting and informative for you as well for us.
We are already looking forward to Valve World Expo 2020 and hope to meet you again at our booth.
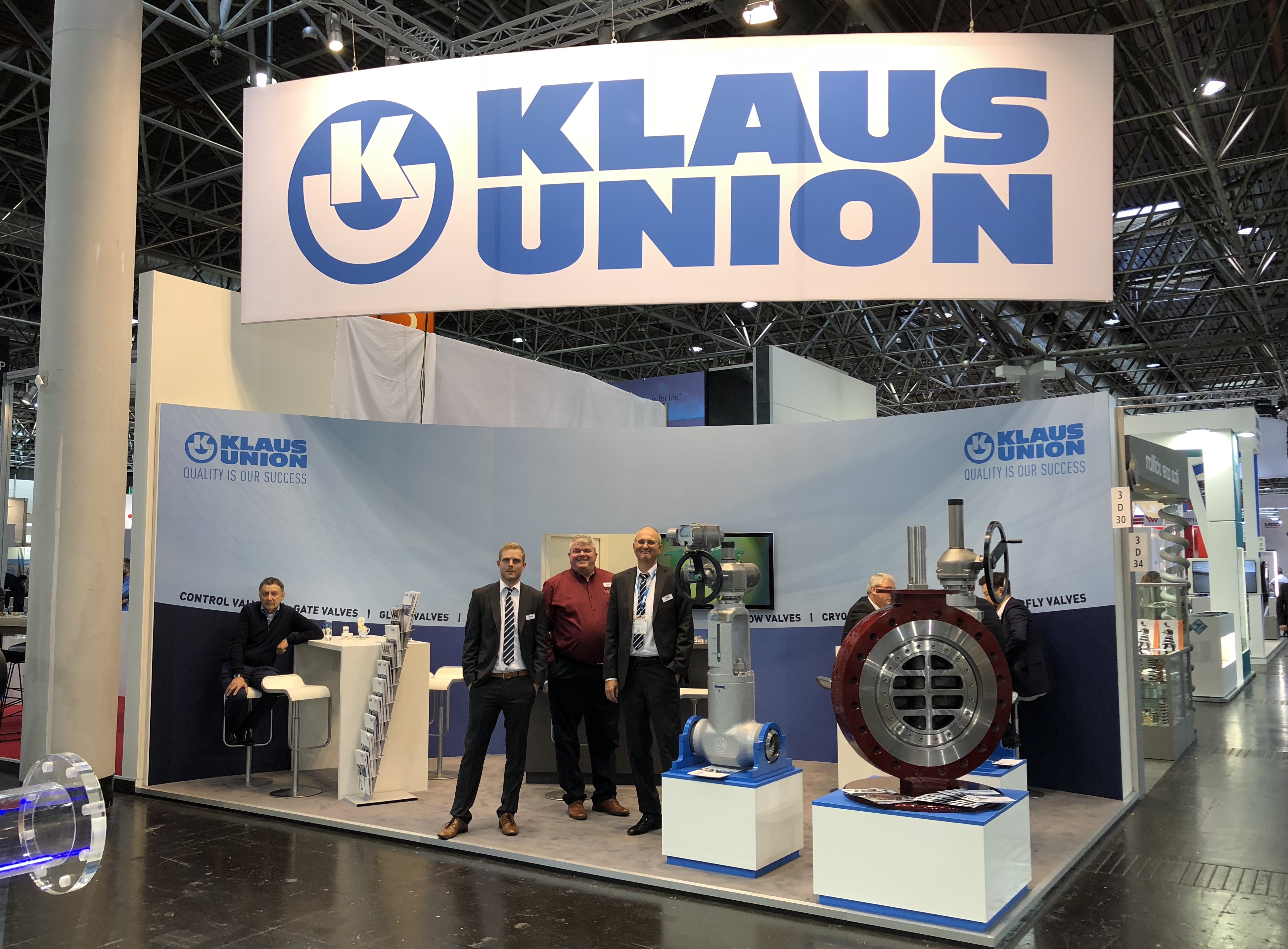
Successfully commissioned
Successfully commissioned
Custom-made submerged pumps
After successfully passing the FAT, these custom-made submerged pumps, type SLM GVTT 080-040-200/3-16E02 ZJ, were delivered to Oranje-Nassau Energie B.V.
The pumps were commissioned in a storage tank farm for butane and propane and will be used for truck loading. Klaus Union faced special project requirements as the existing equipment like a pressure control and level control have to fit on the limited space of the cover plate. Further the pump skids come with explosion proof motors with integrated frequency drives.
To avoid any kind of vaporisation, all pumps are equipped with Zirconium Oxide containment shells. Through the use of these non-metallic containment shells instead of the traditionally used metallic containment shells, Klaus Union eliminates eddy current losses with the corresponding temperature rise in the product and increases the efficiency of magnet drive pumps significantly. As an additional feature, an inducer is installed to substantially reduce the pump’s NPSH3 value without altering other pump characteristics.
The material of the pump is a special low temperature carbon steel and designed for a maximum pressure of 40 bar.
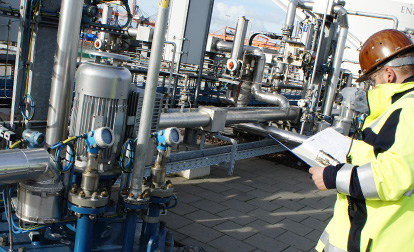
First-Time Delivery
Pumps with double-wall isolation shells transmitting more than 100 kW
After extensive tests and successful final inspection, Klaus Union has delivered 31 centrifugal magnetic drive pump skids for a large-scale project in the USA.
The highlight of this delivery is the special design of the "Secondary Containment" acc. API 685 2nd. Edition in the form of double-wall isolation shells, which are used for the first time at 3.500 rpm with transmission capacities of more than 100 kW! In addition, 3 large pumps (more than 230 kW power consumption) were supplied, which will be operated in parallel at high temperature (> 300 °C) delivering combined nearly 1.000 m³/h.
The magnetically coupled centrifugal pumps type SLM NVO according to ASME 73.3/ISO 15783, SLM AVP according to API 685 2nd Ed. and SLM GVOT are used in a plant for the production of linear alpha-olefins. The pump kits include electric motors, couplings, instrumentation for monitoring, base plates and painting. All equipment was strictly executed according to the project specifications, which were specially created for this complex and demanding large-scale project.
Major Order
42 Pump Units Successfully Delivered
After ambitious testing and final inspection, 42 pump units have been successfully completed for a world scale project located in Saudi Arabia.
These magnetically coupled centrifugal pumps, model SLM AVO acc. ASME 73.3 / ISO 15783, are used in a sulfur recovery unit (SRU) in an IGCC (integrated gasification combined-cycle) power plant and are pumping sulfur enriched solvents.
The pump skids include electric motors, couplings, instrumentation for monitoring with wiring, base plates and painting. All the equipment has been engineered according the project specifications of great complexity and scale.